High-Efficiency Refractory Linings to reduce the impact of Cement plants on Greenhouse Gases emissions through fuels savings
SUMMARY
Cement Industry has a very relevant impact on Greenhouse Gases emissions (GHG) at global level, causing the everyday more obvious Climate Change leading to environmental incidents, affecting our planet and ourselves. The industry is implementing practices aimed to the reduction of emissions, being one of the main initiatives the reduction of fossil (coals) or derived from fossil (petcoke) fuels burned for clinker production, intermediate product for cement manufacture.
Refractory linings at clinker kilns have therefore a potential of beneficial impact on the reduction of GHG emissions causing Global Warming, through the adoption of High-Efficiency Refractory Linings (HERL), minimising the consumption of fossil fuels necessary for clinker fabrication and hence reducing both GHG emissions and variable production costs. HERL investment is quickly paid off thanks to thermal savings, while strategically becomes mandatory in the context of Climate Emergency we live in.
CLIMATE CHANGE CONTEXT
Currently the grave problem of Climate Change has been renamed as Climate Emergency given the evidence of quick global warming of the Earth and the magnitude of its effects on the natural habitats and populated areas, taking place much more often extreme phenomena like massive fires, prolonged droughts, icebergs melting, floods caused by the loss of forest mass, etc.
It is commonly accepted by the Scientific Community that within this 2020-2030 decade Humanity must adopt urgent policies and put in place measures aimed to the sustained reduction of Greenhouse Gases (GHG), main cause of the global warming.
In this context, the Power Generation sector from fossil fuels appears as the major contributor, followed by a series of industrial processes headed by Cement Industry. Cement production contributes with until 8% of global GHG emissions caused by human activity, more than all the worldwide road trucks fleet used for terrestrial transport. Moreover, Cement sector is the second global generator of CO2 and third global energy consumer, which in turn requires a higher utilisation of pollutant power stations.
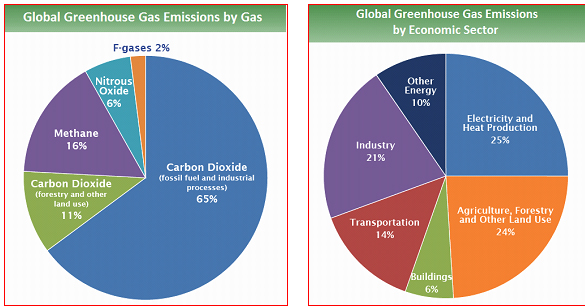
Source : US Environmental Protection Agency
CO2 emitted for civil works concrete manufacture (from which 14% is cement) is estimated as 410 kgCO2/m3 of concrete, in other words, some 180 kg for each ton of concrete (at an average density of 2.3 mT/m3), although the use of fly and wet ashes (more and more scarce due to gradual paralisation of fossil fuels power stations) may reduce these emissions by until a 30%. CO2 emissions due to civil works concrete fabrication is therefore directly proportional to the cement content in concrete. 900 kg of CO2 are emitted for the fabrication of 1 ton of cement, assuming an average of 70% of emissions related to each ton of concrete.
Therefore it is urgent the adoption of immediate measures to revert this trend, which major Cement Groups worldwide are articulating around:
• Optimisation of energy efficiency of the clinker production process.
• Maximisation of waste fuels burning to minimise the use of fossil fuels (petcokes, coals, liquid oils, natural gas).
• Reduction of clinker content per ton of cement through the use of alternative materials replacing clinker and compatible with cement specifications.
• Electric power co-generation for internal consumption of cement plant, usually from spare hot air from coolers, hence reducing the demand of electric power from the grid.
• Development and production of new clinker types, of lower environmental impact and/or higher reactivity.
• Adoption of technologies to capture and/or reuse of CO2 (future).
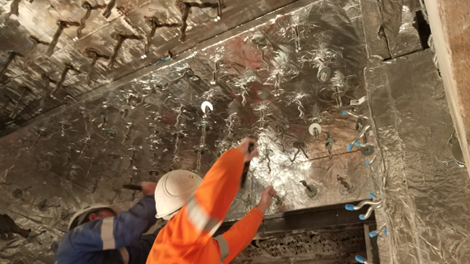
Installation of a High-Efficiency Refractory Lining (HERL)
It should be remarked that these measures are subject to technical and process limitations, conditioning their effectiveness, but much more can still be done within the scope of energy optimisation.
COMPARTE ESTE ARTÍCULO EN TUS REDES SOCIALES
COMPARTE ESTE ARTÍCULO EN TUS REDES SOCIALES
Merry Christmas and Happy New Year 2022
Artículos
INSTALLATION SYSTEMS OF UNSHAPED REFRACTORY MATERIALS (Part 2)
Last week we published the article INSTALLATION SYSTEMS OF UNSHAPED REFRACTORY